Jetzt oder nie: Bettina baut sich ein Ruderboot
Bettina wohnt direkt am Wasser, hat aber kein Boot. Das ändert sie. Sie baut sich unter Anleitung ein „Eastport Pram“.
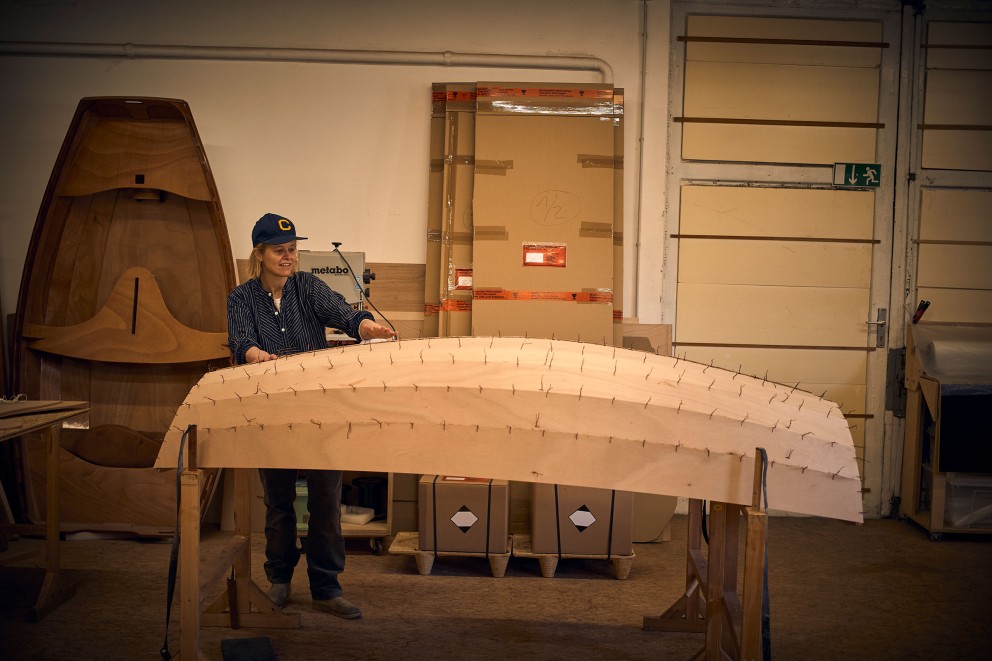
So ein Ruderboot fordert Kraft. Und Ausdauer. Bei meinem letzten Ruderversuch auf dem Berliner Schlachtensee wollte ich die Ruder in der Seemitte am liebsten wegschmeißen – und meine Arme gleich hinterher. Habe ich aber nicht. Im Gegenteil. Ich habe ihnen eine neue Herausforderung gesucht: schleifen, bohren, feilen, stitchen, kleben. Stundenlang, tagelang. Ich will ein Ruderboot bauen. Mein Ruderboot. Schließlich ist ganz Berlin voller Wasser, ich könnte sogar von mir zu Hause mit dem Boot direkt ins Büro rudern, und das werde ich auch.
Bettina Lüke
Ich habe rausgefunden, dass es ganz in der Nähe von mir in Berlin-Lichtenberg bei Lutz Berger von Berger Boote dafür Bausätze gibt inklusive Workshop. Lutz wird mir in seiner Werkstatt helfen, mein Ruderboot selbst zu bauen. Ein „Eastport Pram“. So heißt das Modell.
Zur Sicherheit prüfe ich anhand der Checkliste auf der Website, ob das Projekt und ich zusammenpassen. Meine Erfahrung mit Holz ist begrenzt, aber ich beschließe, dass ich das schon schaffen werde.
Gesagt, getan. Am nächsten Tag stehe ich bei Lutz in der Werkstatt. Das Material liegt schon bereit. Ich zähle Planken, Heck, Bug und Flächen, alles aus Okoumé-Sperrholz, plus kleinere Teile, deren Namen ich noch nicht kenne. Dazu Glasfaser, Epoxidharz, Härter, Holzmehl. Und Kupferdraht. Die Technik, mit der ich mein Boot baue, heißt „Stitch & Glue“, zuerst wird mit Draht „genäht“, dann geklebt. Stitch für Stitch.
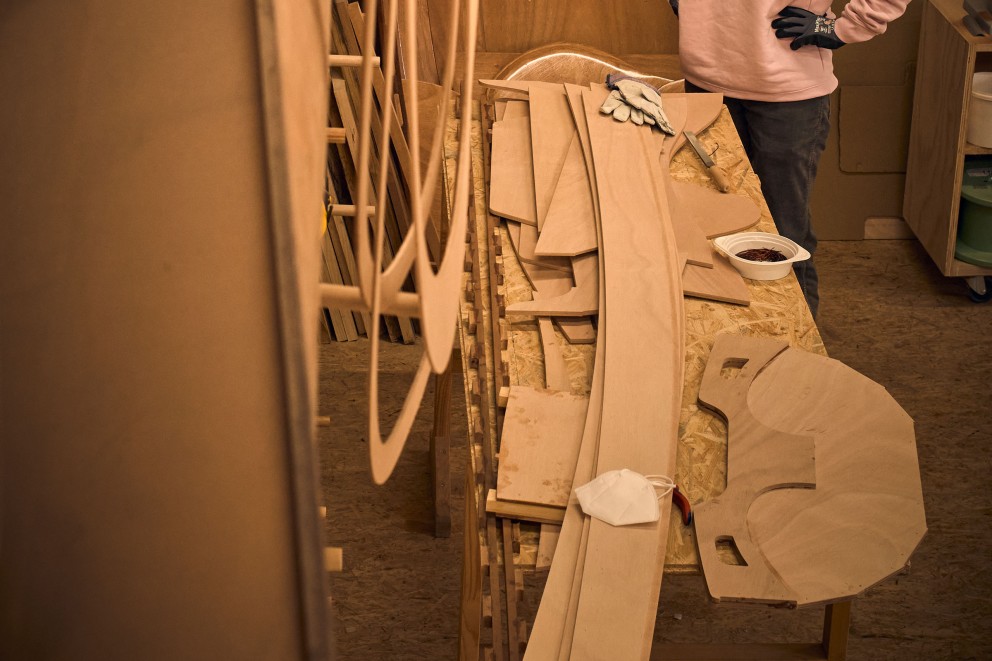
Ahoi, los geht’s. Der Bootsboden wird mit zwei Planken verbunden – es sind die ersten von fast 250 Kupferdrähten, die ich, zunächst handfest, in die vorgebohrten Löcher setze. Dann Heck und Bug. Toll: Nach ein paar Handgriffen sieht es schon wie ein Boot aus. Und das soll sechs Tage dauern? Das sagt zumindest Lutz. Und er soll Recht behalten.
Bevor es weitergehen kann, feile ich die unteren Einbauten zurecht, alles soll möglichst bündig sein. Dann drahte und drahte ich weiter. Erst die Einbauten, dann die anderen Planken, zuletzt muss ich alle Drähte mit der Zange verdrillen. Damit ist der Stitching-Teil beendet – beinahe jedenfalls.
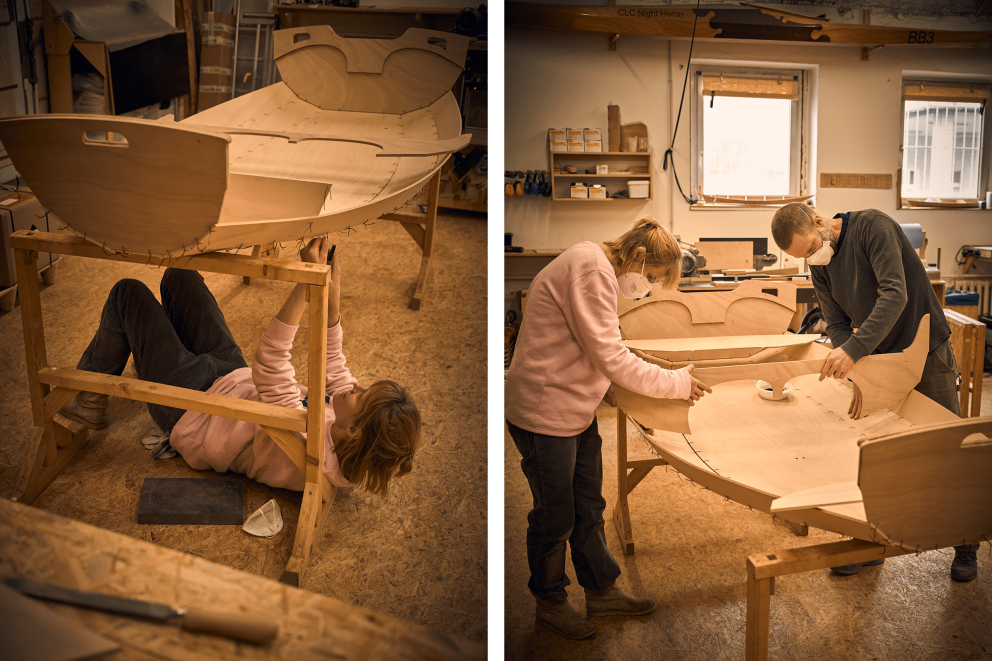
Jetzt geht es los mit dem „Glue“. Epoxidharz und Härter müssen präzise vermischt werden. Ich muss ein bisschen üben, bis ich es raushabe: Ich darf weder zu stark kippen noch zu viel tröpfeln. Falsche Mischungen, sind sie einmal aufgetragen, können das ganze Boot ruinieren. In den Mix rühre ich nun mit dem Spatel Holzpulver, bis er eine erdnussbutterartige Konsistenz hat.
Die Masse kommt nun in einen Spritzbeutel. Ich erinnere mich, dass ich mit meiner Oma so riesige Sahnetorten verziert habe – vor langer Zeit. Also alles Richtung Beutelspitzedrücken, mit möglichst wenig Luft, die Spitze des Beutels kappen, und schon kann es losgehen: Zentimeter für Zentimeter drücke ich die Masse in die Fugen zwischen den Planken. Dabei spare ich die Verdrahtungen aus. Die Drähte müssen später wieder raus.
Mit der Spachtelmasse verfuge ich auch die anderen Zwischenräume und ziehe die ersten Kehlen – sanfte Rundungen – an den Einbauten. Der Tag ist fast vorbei, der erwartete Muskelkater bleibt aus.

Am nächsten Morgen ist die Kompositmasse ausgehärtet. Die Drähte können raus. Mit der Zange durchknipsen und rausziehen. Das Wichtigste aber: Alles hält! Mein Boot sieht schon wieder ein bisschen „fertiger“ aus. Doch das täuscht … vier Fünftel der Arbeit liegen noch vor mir. Mit der Japansäge schneide ich den Schwertkasten zurecht. Ich nenne ihn „Sitzstütze“. Dank des besonderen Sägeblatts geht es ratzfatz und wird vor allem glatt.
Glatt soll auch der Kleber sein, den ich auf die Klebekanten auftrage, doch zuerst wird gebohrt, denn die Stütze wird nach dem Kleben mit Messingschrauben an Mittelteil und Boden befestigt. Es ist nicht ganz so leicht, die Schrauben von unten festzuziehen. Dann klebe ich mit Kreppband die Kante ab und ziehe Kehlen um die Bodenkanten.
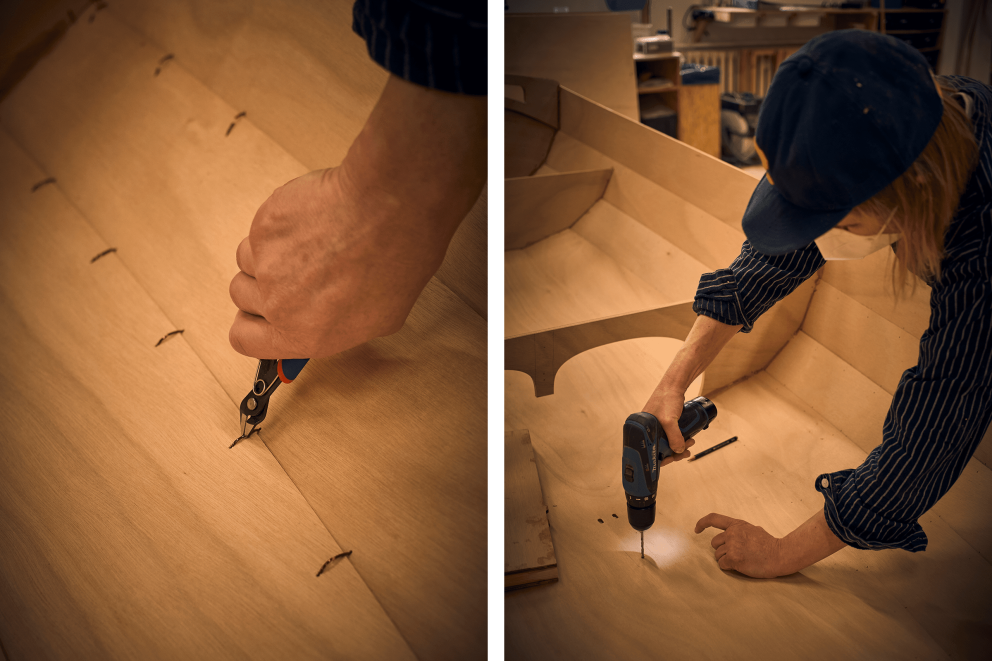
Am dritten Tag geht endlich das große Schleifen los. Ich säge die Planken-Überstände an Bug und Heck ab und schleife mit dem Exzenter alles flächig. Für die Außenfugen der Planken muss ich aber Schleifpapier nehmen. Dann folgt meine erste Begegnung mit dem Material Glasfaser. Ein Teil des Stoffes wird mit einer Spezialschere auf die Unterbodengröße zugeschnitten und dann drapiert. Meine Angst, Wellen zu machen, erweist sich als unbegründet, es geht ziemlich gut. Das Gewebe tränke ich mit Epoxidmischung, diesmal ohne Holzpulver. Lutz’ Tipp: in der Mitte anfangen und nicht zu nass werden, die Struktur des Glasfaserstoffes soll erkennbar bleiben. Im Anschluss wieder Spritztüten-Klebeaktion: Ich ziehe Kehlen an den zuvor geschliffenen Außenfugen. Für die Nacht ist wieder Trockendock angesagt.
Die Glasfaserschicht auf der Unterseite ist am nächsten Tag superhart, und ich schneide die Überstände mit dem Cutter ab, die Kleberänder schleife ich. Nachdem das Boot umgedreht ist, wird die Bodenkehle innen geschliffen, dann der Innenboden ausgesaugt. Jetzt kommt hier die Glasfaser plus Epoxidmischung rein, auch über die unterste Planke. Damit es akkurate Übergänge gibt, klebe ich die Plankenkanten mit breitem transparentem Tape ab. Wichtig: an den Enden Laschen machen, damit das Band später sauber und vor allem restlos entfernt werden kann. Wegen der Einbauten ist das Zuschneiden und Einpassen diesmal heikel. Und tatsächlich habe ich zu schief geschnitten. Es ist eine Lücke entstanden. Was jetzt? Lutz sagt, die circa zwei Zentimeter sind okay. Ich bin erleichtert. Das Auftragen der Epoxidmischung ist diesmal ebenfalls schwieriger. Ich versuche Luftbläschen und Wellen zu vermeiden oder auszustreichen und hoffe, dass es klappt. Sonst muss ich die Dellen später wegschleifen.
Weil ich noch Epoxid übrig habe, gebe ich den Bänken und der Kielhacke, die dem Boot Stabilität gibt, schon mal jeweils eine Schicht. Ich ahne nun, wie das Holz am Ende aussehen wird.
Die letzte Aufgabe für heute: die Bordleisten. Die beiden Latten sind aus Mahagoni und werden mit der Epoxidmischung zusammengeklebt. Mit einer weiteren Klebeschicht sollen sie dann am Boot angebracht werden, und das ist jetzt wirklich etwas, was ich allein nicht schaffen könnte. Lutz hilft mir, sie mit Klemmen zu fixieren, und zwar bündig, damit hinterher nicht beigeschliffen werden muss.
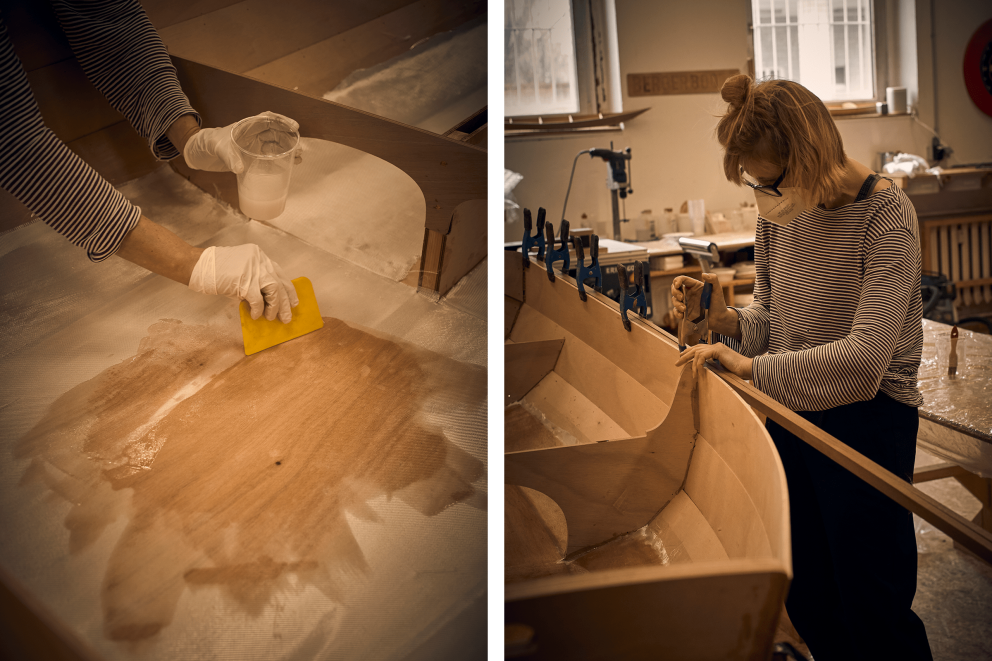
Ob es hält, erfahre ich nach dem Aushärten. Vorsichtig löse ich die Klemmen und Zwingen.Jawoll! Ich säge die Überstände ab, und dann kommt wieder der Exzenterschleiferzum Einsatz, bis die Leisten und der Bootsrand eine einheitliche Fläche bilden.Was kann ich noch abmachen? Die Kanten der Glasfaser innen wieder mit dem Cutter.Dann das Klebeband. Akribisch kratze ich die Reste weg und schleife schon mal ein wenig Unebenheiten aus.
Mit Schleifpapier gehe ich danach über den geharzten Unterboden und gleich auch nochüber die Außenränder an Heck und Bug, ebenso über das Skeg, das ist die Ruderleitflosse, bis es passgenau auf dem Unterboden aufliegt. Das Skeg schraube ich dann zusammen mit den beiden Bodenschutzleisten am Bootsboden an. Bohrlöcher einzeichnen und vorbohren, Klebemasse auf die Kanten aufgetragen, dann packt Lutz noch mal mit an: Beim Anschrauben müssen wir das Skeg und vor allem die Leisten ganz fest andrücken, damit ich von unten schrauben kann – ziemlich sicher der größte Kraftakt im Projekt. Als alles sitzt, ziehe ich wieder Kehlen drum herum.
Dann wird wieder geschliffen, von Hand und geduldig, bis alle Kehlen glatt und die Flächen ordentlich aufgeraut sind. Alle Klebereste und -flecken müssen weg, Ecken und Kanten gerundet und geglättet werden. Puh! Um zumindest in Zukunft nicht immer auf die Kraft meiner Arme angewiesen zu sein, bringe ich die Platte für einen Motor am Heck an.
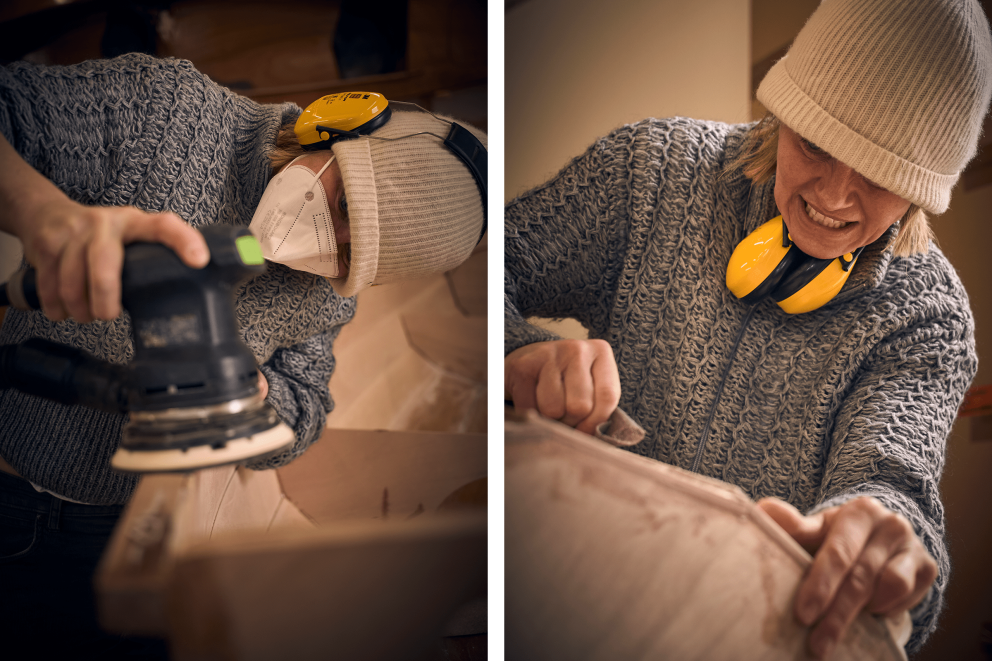
Dann kommt eine Arbeit, die weniger Geduld erfordert: Epoxid-Härter-Mischung auftragen. Für die Kanten nehme ich den Pinsel, sonst die Rolle, so geht es schön schnell. Nach einer Schicht Epoxid sieht das Boot auch von innen schon fast seetüchtig aus. Ist es aber noch nicht. Die Sitze! Deren Klebeflächen zeichne ich ein, bevor sie mit Klebemasse bestrichen werden. Passen sie? Tun sie. Wir beschweren sie mit Gewichten. Dann müssen die Kanten wieder verkehlt werden.
Und das ganze Boot braucht eine zweite Lage Epoxid, damit es nicht nur hält, sondern ich es auch meinen Kindern vererben kann. Und wenn das trocken ist, geht es ans Lackieren. Das ist wichtig für den Sonnenschutz. Vielleicht können die Kinder mir dabei dann schon mal helfen. In der Zwischenzeit überlegen wir uns, welche Farben wir nehmen. Und dann braucht mein Boot nur noch einen Namen …
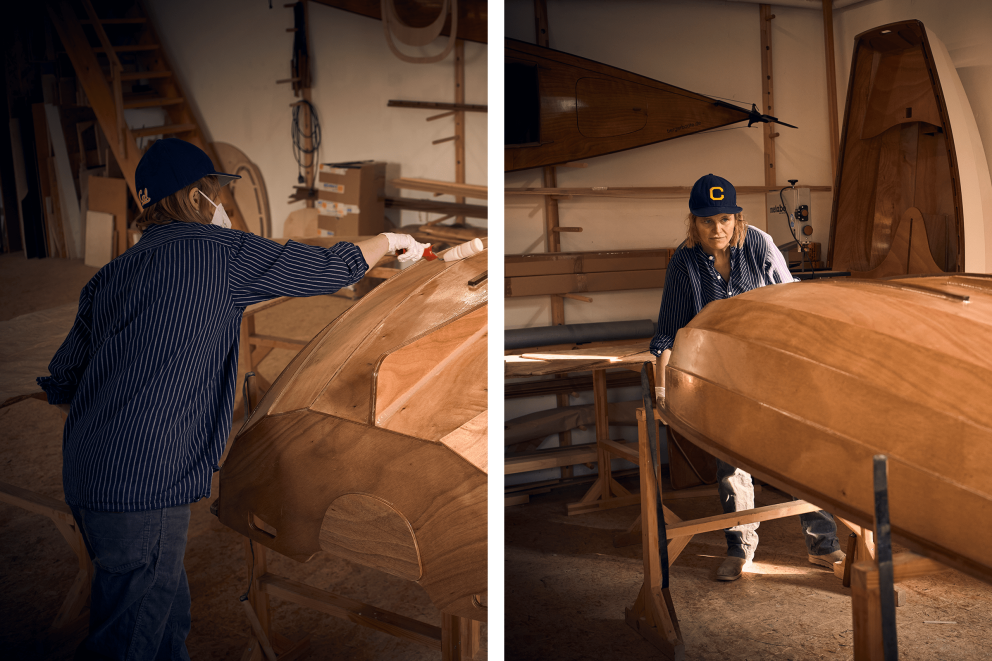
Man kann das „Eastport Pram“ übrigens auch mit einem Segel aufrüsten. Und wer wirklich alles selbst machen mag, bestellt sich einfach nur den Bauplan. Überlege ich mir dann für mein nächstes Boot, jetzt, wo ich’s kann.
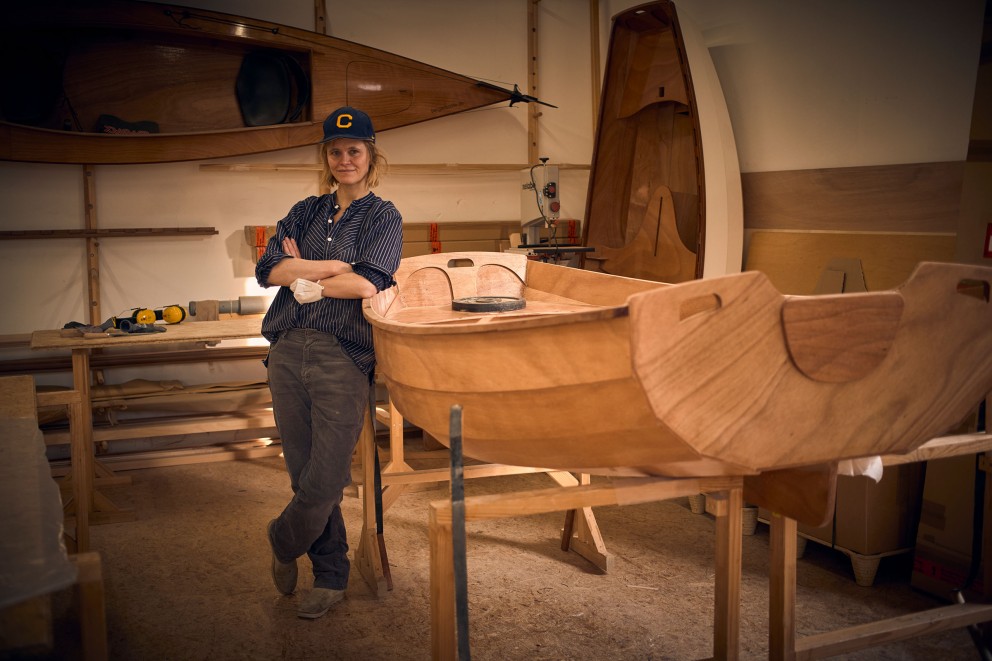
Text: Bettina Lüke | Fotos: Jannis Chavakis